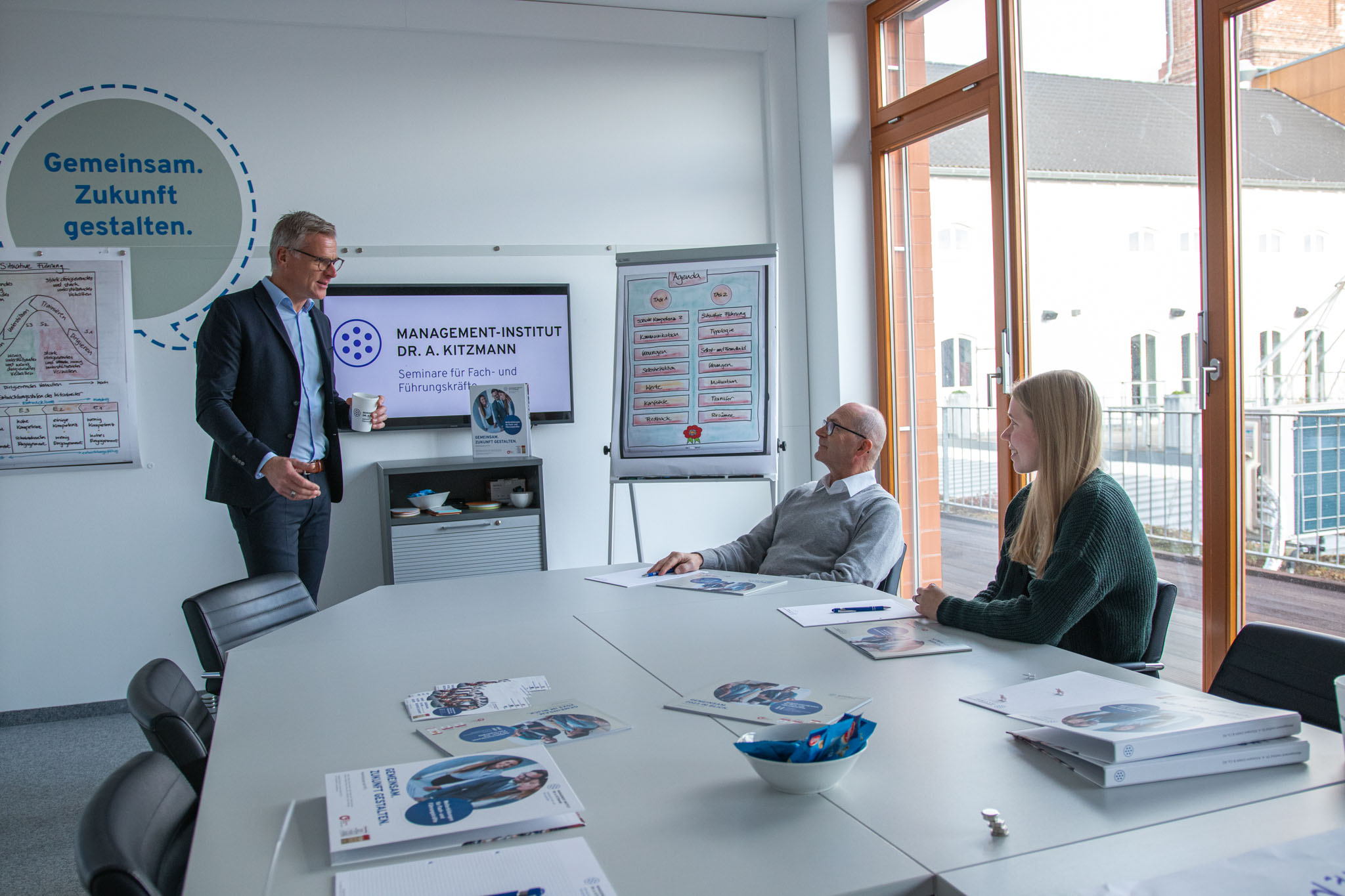
Case study: Better self-organization through modern methods tools
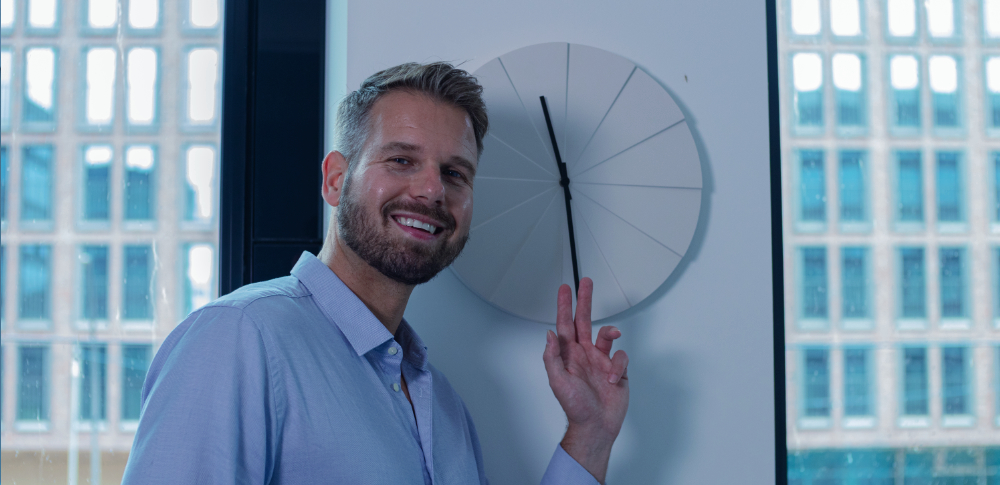
1. Description of the initial situation
This company specializes in the production of rolling bearings, spherical plain bearings and bushings. Customer contact is direct and usually requires a customized solution, fast reactions and very good internal coordination. Here it is particularly important to act quickly, document well and make no mistakes. Specialized inquiries in particular require very clear communication. The core objective of the workshop was therefore for all participants to learn how to better organize themselves with the help of Microsoft Outlook.
2. Goal of the customer
The company grew expeditiously in Germany because of the market gap. A complex chain of internal and external communication channels was created due to the high demand for products. The increased volume of tasks created the need for better use of tools (in this case: Microsoft Outlook) as well as personal self-organization. The goal for the workshop was to achieve a better self-organization, better lines of communication and a higher efficiency in communication, by optimizing the usage of existing tools.
3. Format of the course (on-site)
In order to ensure maximal interaction, the on-site format was chosen. The training took place in the company. The largest meeting room was used for the entire day. All of the participants' problems were discussed in order to find the most personalized solutions. Their implementation started directly after the seminar ended. A target list, necessary for the future adjustments, was also established.
4. Result and future prospects
The entire course was evaluated by the Kitzmann Institute and by the company. The seminar in its entirety was deemed a success. The high practical relevance and the direct applicability of what was learned were particularly appreciated. Furthermore, it was directly decided that an additional day will be booked for the future development of the company, so that the positive change doesn't stay a one-time event, but rather becomes a part of the continuous improvement process (CIP).